High Pressure Tank Farm

The initial design of a network of pipes running from the high-pressure tank farm made no provision for corrosion and erosion between the pipes and their supports. Pipes were simply rested on metal supports and over years the corrosion reduced the wall thickness of the pipes at these points. Some touchpoints were also welded to the supporting I-beams which traps water which greatly accelerates corrosion.
​
The Ovolifts system was used to raise entire racks of pipes in a single lift whilst keeping within limits of the allowable bending stresses of the pipes.


The large number of contact areas and the difficulty in accessing these regions meant accurate wall thickness measurements could not be taken. Wall thicknesses were estimated based on a worst-case scenarios and pipes were reclassified to lower operating pressures at the expense of a lowered production output.
​
The challenge was to provide access to multiple contact areas for inspection crews to take actual wall thickness measurements using an ultra-sound device and to measure pitting. At the same time crews would need access to conduct maintenance across all the supports.

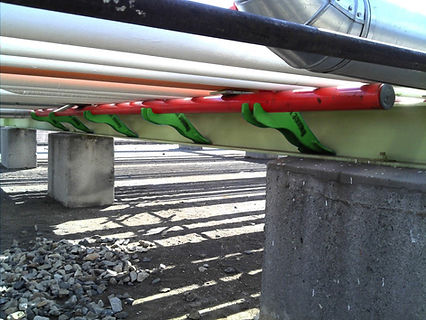
Over a period of 3 months, 1200 pipe contacts were lifted 2” from their supports, sufficient for inspection crews to collect valuable wall thickness and pitting data. Whilst the pipes were raised, maintenance crews sandblasted both the pipes and the supports, applied a fresh coating of paint and glued a teflon spacer to the beam before lowering the pipes down onto the teflon spacers which would eliminate further metal on metal corrosion and erosion.